Primary Navigation
Buying Guidelines
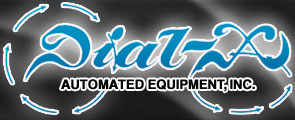
Consult with a reputable automation vendor with the capability to take full responsibility for designing and building automation equipment, building vibratory feeder bowls, designing and building controls for the automation equipment, as well as the electrical and pneumatic components of the automated machinery. A single source automation vendor will result in less expensive automation equipment for you with more productive automation, resulting in fewer service calls. If, however, service to your automated equipment is required, the automation vendor should also be capable of servicing your automated equipment in a timely manner.
In selecting an automation vendor for your automation project, you should contact previous customers of the automation vendor and ask about the quality of the equipment, the service provided, and the training of their personnel, prior to sending a request for a quotation to the automation vendor.
Select approximately three reputable automation vendors when requesting a quotation for your automation project. Send parts (assembled components and unassembled components) and ask for budgetary pricing. This will save both yourself and the automation vendor time in determining if the automation project is viable.
If at all possible, you should visit the automation vendor's facility to review the automation equipment being built on their floor at that time. Acquire a list of the automation vendor's previous customers in your area. If possible, visit these customers to view the automation equipment in action.
Request a Certificate of Insurance from the Automation Vendor
If the automation project is viable and you have received budgetary pricing from the vendor, you should request that the automation vendor visit your facility to review the automation project further. This meeting should include the automation vendor, two individuals in management, two individuals in maintenance, and two individuals from the assembly department. It is essential to have the input of all departments to assure a successful automation project.
Supply the automation vendor with the following:
Assembled components - as the automated system will produce.
Specifications of any equipment your company prefers. Keep this short but complete. Be sure to include the color you request the automated system be painted as well as any other options specific to your company.
Two sets of updated prints of components; making notes on print if any of the parts are not to contain flash/burrs or any other imperfections.
If molded parts, samples from each cavity are required.
Provide information that your Quality Control Department would be looking for during assembly at your facility.
Management, Maintenance and Production personnel should discuss the project in its entirety prior to issuing a purchase order for the automation project.
Schedule a chain-of-command, agreeable with your company and your automation vendor. There should be only one person from each company communicating with one another, with a second person possibly designated as backup contact.
At the time a purchase order is issued, inform your Management, Production and Maintenance departments of the automation vendor selected for the project.
At the time your selected automation vendor requests your presence for design review, representatives from your Maintenance, Production, and Engineering departments should all be present.
Run-off of the equipment at the automation vendor's facility should include a representative from your Maintenance, Engineering, and Production departments. Any production parts ran at this time should be given directly to your Quality Control Department for their inspection.
Delivery of your automated equipment should be made by a reputable machinery rigger and should be shipped from the vendor's facility directly to the customer's facility. Equipment should be moved on an air-ride tractor and trailer only.
When equipment is wired and large enough, an airline is ran to the system; vendor should be notified of this. You should have the same parts on hand as the automation vendor had on their floor for run-off of the system. Any and all personnel that were involved with the approval of the design and run-off at the automation vendor's facility should be involved, as well as one Production person from each shift running the new automated system.
Immediately following your onsite on your new equipment by the automation vendor, it is likely that you will have some minor problems which may require adjustments of one sort or another. You should document any/all problems incurred over the first two week period of production, describing them in detail. Approximately two weeks into running the system, contact your automation vendor and request that the automation vendor schedule a visit at your facility to discuss all problems documented. A copy should be sent to them for their review prior to the visit. Major problems, however, should be dealt with immediately.
For further information or a free quote on your automation projects, contact Dial-X Automated Equipment, Inc.